“机器人+”典型应用场景案例集--矿山领域机器人典型应用场景:地下竖向工程智能掘进
编者按:为加快矿山领域机器人应用推广,更好服务矿山安全高质量发展,国家矿山安全监察局安全基础司、工业和信息化部装备工业一司联合开展了矿山领域机器人典型应用场景遴选工作,确定推广31个典型应用场景、66个场景实例。现组织中国软件评测中心梳理66个场景实例的先进经验及应用成效,在“机器人+”供需对接与应用推广公共服务平台及相关微信公众号开展持续宣传,以更好推动典型应用场景的复制与推广。矿山种类:非煤矿山 |
应用场景:掘进 |
场景实例:地下竖向工程智能掘进 |
机器人产品及制造单位:智能钻井机器人,湖南创远高新机械有限责任公司 |
应用单位:山西紫金矿业有限公司、安徽开发矿业有限公司 |
天井钻机强大的破岩成孔及反向扩孔能力,能够有效解决复杂地质条件和有限作业空间的施工问题,在矿山领域竖向工程掘进中得到广泛应用。
竖向工程施工危险系数高,人员施工效率低下。地下矿山竖向工程施工以传统的普通法、吊罐法、爬罐法等人工半机械化的钻爆法方式为主,成井质量差,且效率不高。施工过程中,人员常受到炮烟、落石、粉尘、噪音、触电、高空坠落和淋水等威胁,作业安全性低。
传统天井钻机无法满足智能化掘进施工需求。传统轨轮式天井钻机转场作业时,需要先拆机,人为浇筑地基,提前铺设轨道,借助外部牵引装置实现移动和完成组装后才能进行掘进作业,且缺乏对各种复杂地质岩层自主作业控制,针对不同岩层条件,无法实现钻进模式的自动选择、最佳作业参数确定以及过程中的卡钻故障自判断、自决策与处理。
传统天井钻机岩层适应性差,破岩能力有限。传统天井钻机反提力和回转扭矩较小,钻杆抗拉强度不高,配套使用的钻具,在结构设计和热处理工艺方面尚不够完善,使用寿命短,载荷低,针对硬质岩层,破岩作业难度大。
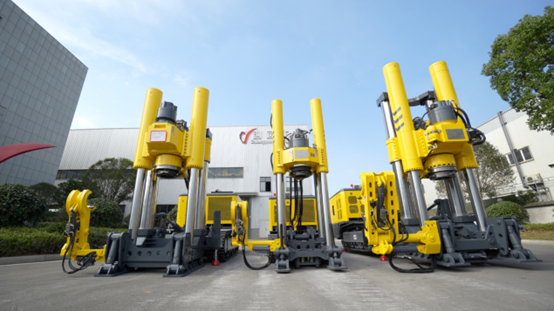
智能钻井机器人是用于地下矿井钻进的智能化装备,具有履带式行走、自动接卸钻杆、快速定位、自主导孔、扩孔等功能,可实现在地下竖向工程中的智能化与无人化掘进作业。智能钻井机器人采用动态插板、自动寻位、钻杆自动输送等技术,实现了智能化接卸钻杆,使用钻机一体化行走系统和液压支柱快速定位系统,无需拆装转场和浇筑地基,减少了转场立机时间,实现“即达即用”,有效提升施工作业效率。搭建“立机定位、钻杆输送、钻杆接卸、智能掘进”生产过程的数学模型和优化算法并研发了钻机专用的IDOS3.0智能作业系统,实现了地下竖向工程掘进全流程无人作业。研发的新型钻杆螺纹结构、高强度钻杆材料和热处理工艺,提高了钻具强度,实现了天井钻机全岩性破岩作业。智能钻井机器人已广泛应用于中国五矿集团、中国电建集团、紫金矿业集团、中铝集团、酒钢集团、鞍钢集团等国内众多龙头矿山企业,并出口至俄罗斯、塞尔维亚、墨西哥、吉尔吉斯斯坦、塔吉克斯坦、圭亚那等国。目前,已销售100余台智能钻井机器人,销售收入超4亿元,近三年企业平均复合增长率超39%,解决就业200余人。在阿舍勒铜矿应用2台智能钻井机器人,应用后,综合工效较同类产品提升6倍,用工人数减少80%,作业成本减少50%;在墨西哥托雷翁(Mexico Torreon)应用2台智能钻井机器人,应用后,用工人数减少50%以上,工效提升2倍;在北京金诚信公司应用5台智能钻井机器人,应用后,每米作业节约电费两百多元;在山西紫金矿业应用2台智能钻井机器人,应用后,完成208米天井的无人化自主导孔/扩孔作业,用工人数减少50%以上;在酒钢镜铁山矿业天井应用2台智能钻井机器人,应用后,掘进时间节约1-2周;在安徽开发矿业应用5台智能钻井机器人,应用后,完成3862米天井施工,用工人数减少50%以上。
特别声明:
本文转载仅仅是出于传播信息的需要,并不意味着代表本网站观点或证实其内容的真实性;如其他媒体、网站或个人从本网站转载使用,须保留本网站注明的“来源”,并自负版权等法律责任;作者如果不希望被转载或者联系转载稿费等事宜,请与我们接洽。
更多精彩内容,关注“传煤”微信公众号,或点击“期刊群”免费获取科研论文
用微信扫描左侧二维码,关注“传煤”公众号,第一时间获取煤炭行业新鲜资讯,享全方位煤炭科技知识信息服务。